- FMA
- The Fabricator
- FABTECH
- Canadian Metalworking
Smart Steel
Mold steel considerations for buying the best in performance
- By Jim Anderton
- June 17, 2014
- Article
- Fabricating
There are a thousand ways to spell “trouble” in plastic mold manufacturing and when it strikes, the finger pointing begins in earnest. The material is always a suspect, which is natural when dealing with defects, but there’s a lot going on in a cavity or block between skinning the steel and final benching. Here are some problems and causes of common issues:
SOFT AREAS ON THE MOLD SURFACE
Soft regions in the mold surface post heat treating can affect all performance aspects of the mold, but in particular lower wear resistance and reduced life are the biggest. Some basic causes are:
- Poor or no surface preparation prior to heat treating
- Incorrect or inadequate heat quench cycles
- Wrong or contaminated quenching medium
- Mismatch between desired hardness spec and steel or process
How can we prevent these problems? Oxygen is the enemy of most processes that alter material properties, and mold steels are no exception. Oxide layers are a bad thing and should be removed, and optimal heat treatment should occur either in a vacuum, or controlled atmosphere oven. Wrong or inadequate heat/quench profiles occur due to two primary factors. The first is specification related. Most mold builders have a desired surface hardness they need for achieving polishability, but rarely specify a particular heat treat methodology. Lead times are short these days, and the need to turn around mold parts quickly results in pressure to cut corners in cycle times or substitute marginal processes to meet delivery deadlines. Done properly, there’s no way to cut corners in heat treating; switching suppliers to a treater or that promises very ambitious turnaround time may suggest that they’re shaving minutes or omitting entire steps in a process that often takes tens of hours.
The other issue is based on material selection. The mold maker may have a desired hardness, and even specify a particular heat/quench profile, but if the chosen alloy is non-uniform, dirty, or is marginal in its hardenability to the desired level, problems are highly likely. Even a contaminated or incorrectly chosen quenching medium can have a major effect. It’s important to establish a good working relationship with the treater to understand the variables.
CRACKING
Large or small, cracks on extensively machined mold part are frustrating and expensive. The nature of the heat treating process is that the soak at a specified elevated temperature develops and homogenizes a desired microstructure, which is then frozen in by quenching. The key factor in quenching is that the rate of cooling is critical, rather than the final temperature. This is why different steel grades and different hardness levels require a variety of quenching media. Steels are crystalline solids, and the rapid rates of cooling associated with hardening seriously stress the material. Even worse, mold parts are not perfectly uniform, so varying section thicknesses cool at slightly different rates, introducing stresses that can both crack and distort the part. Some causes are:
- Cold plastic deformation and residual stresses in the part
- Complex part shape than consistent cross-sectional thicknesses
- Failure to remove the white layer on EDM parts
- Incorrect heat/quench profile for the steel chosen
- Inadequate or no stress temper before heat treatment
All machining processes deform the steel to some extent, and residual stresses have to be relieved to prevent later cracking or deformation, especially if machining processes are aggressive and/or the material selection is susceptible to stress cracking. Modern alloys are harder, more complex and high productivity mold making uses very aggressive cutting profiles with high feeds and speeds all of which combine to put considerable stress into the part. Cavities are more complex than ever with little consistency in wall thickness, making it impossible to achieve exactly the same quenching conditions uniformly throughout the part. Experienced heat treaters will spot this problem before they treat, and can compensate to some extent (by damming or plugging holes for example), to slow heat soak and cooling in some critical areas. Similarly, a good heat treater will spot a mismatch between the requested specification and material selection and part shape. Sometimes it’s simply not possible to safely achieve the hardness requested without a serious cracking risk. A stress relieving heat is a good practice, as is mold design that takes steel grade selection and heat treating into account. And like the soft spot problem, clean, uniform material is essential.
PROCESSES FOR CLEAN, CONSISTENT METALS
Great molds always start with highly uniform and homogenous metal alloys. One process that helps achieve super clean steel is electro slag remelting or ESR. Electro slag remelting is deceptively simple. In a water cooled ingot, a consumable electrode is re-melted in contact with a molten slag bath inside the crucible. Electric current passing through the electrode provides the heat source, and as the electrode melts and the molten metal passes through the slag layer, production of sulfur and oxygen occur chemically. Another process, vacuum arc remelting is similar. In VAR, a source electrode is also melted by electric current in a crucible, except under a high vacuum. The crucible is water cooled and the ingot grows from the bottom up as the arc zone melts away the source electrode. The vacuum allows strong degasification before the metal solidifies resulting in very homogenous clean metal with minimal oxide content. Both processes give better hot and cold workability superior mechanical properties. Disadvantages to the processes are a limit to the size of bar due to size constraints on the crucible, and some waste as the ends of the ingot are often sawed away to ensure complete uniformity throughout the block (Fig. 1).
Another high-tech process getting lots of attention today is powder metallurgy. Powder technology works by compacting superfine metal powders and then firing the green compact in an oven to center the particles into a solid mass. With a very fine very uniform particle size, grain boundary growth is also consistent, producing a block with essentially identical mechanical properties throughout. Sintered powder processes are popular for carbide materials, but advancements in vacuum and electroslag processes make remelted product a cost-effective alternative for even demanding applications like lens and die casting molds.
HARDENING IS STILL KEY
The hardening process is still key to the production of long life molds, regardless of the starting metallurgy or machining processes. Despite its importance, the hardening process is still not well understood by many mold makers. Michael Schmidt, Division Manager, Bohler-Uddeholm Thermo Tech relates: “heat treaters have to be conscious of the geometry of the part and how it was machined. Heat treatment almost always results in some form of dimensional change. Our rule of thumb is typically one and a half-thousandths per inch, per side… that should be the minimum amount left on the steel when it comes for heat treat. This should provide adequate stock to allow for proper clean up afterwards.”
In the 1990’s surface hardness was commonly 28- 32HRC, but today its common to harden to 34 HRC or higher. The higher surface hardness improves polish ability, but over polished surfaces are still at risk of pitting due to carbide pull out during the final stages of benching. Higher core hardness is another reason for higher Rockwell numbers; today’s tools are larger, more complex and necessarily more expensive, so mold life is more important than ever. As molding toolmakers demand higher and higher through hardness, heat treaters now commonly use vacuum and a multiple stage heat treating process involving step heating with hours long hold times at preset temperatures, as well as interrupted quenching cycles, freezing intermediate microstructures than reheating and quenching again to a final, fine microstructure. These processes are more involved, more expensive and just as importantly in a fast turnaround shop environment, take time. For step heating and interrupted quenching processes, cycle times can be in the tens of hours, days really, meaning time in a vacuum oven is apportioned by a strict schedule. It’s important to work with the treater to allow adequate lead time to get critical parts through the process and into the finished mold in time to meet delivery schedules.
It’s also important for the mold maker to thoroughly understand effective heat treating on their material. According to Schmidt, “There are grades that may be more susceptible to movement, some more susceptible to shrinkage and some to growth….these are variables that must be factored in. For customers that do repetitive work, they may experiment with the first few tools or components and see what the trend is after heat treating, then adjust all subsequent orders accordingly. Some companies for example know how much a hole will change in size for a given heat treat process based on the historical data, so they leave a very specific amount of overstock for finish machining based on that knowledge.”
Prehardened material can eliminate many of these problems, and with modern insert technology, it’s possible to machine very hard materials cost effectively, but prehardened metal doesn’t always eliminate the need for post treatment. Schmidt adds, “I think it’s a balancing act depending on the job itself and to some degree how much money you have in that job. Inserts and modern cutting tools can definitely machine through hardened steels better, but there’s a definite difference between a hardened H 13 which may be 46 HRC, versus D2 or high-speed steel at a 60-62 HRC, the latter being much more difficult. A P 20 with a mid-30s hardness naturally is easier to machine, something that should be taken advantage of. Where it gets tricky is when you work with hardness’ entering into the high 50’s (HRC) and above.”
About the Author
subscribe now
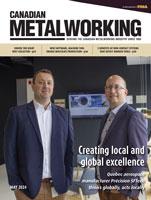
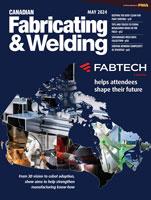
Keep up to date with the latest news, events, and technology for all things metal from our pair of monthly magazines written specifically for Canadian manufacturers!
Start Your Free Subscription- Industry Events
Automate 2024
- May 6 - 9, 2024
- Chicago, IL
ANCA Open House
- May 7 - 8, 2024
- Wixom, MI
17th annual Joint Open House
- May 8 - 9, 2024
- Oakville and Mississauga, ON Canada
MME Saskatoon
- May 28, 2024
- Saskatoon, SK Canada
CME's Health & Safety Symposium for Manufacturers
- May 29, 2024
- Mississauga, ON Canada