- FMA
- The Fabricator
- FABTECH
- Canadian Metalworking
Success by sintering
SLS technology promises to change metal part manufacturing forever… will it live up to the hype?
- By Jim Anderton
- September 18, 2014
- Article
- Metalworking
It seems too good to be true: complex parts without machining, appearing almost out of thin air right before your eyes. While the technology is in its infancy from a production perspective, years of use in prototyping has brought selective laser sintering (SLS) into the forefront among metal additive manufacturing processes. The process is deceptively simple: successive layers of metal powder are deposited in patterns corresponding to lateral slices of the three dimensional part, while a laser beam heats the line of deposited powder, causing a localized melting of the powder. The laser is key, inputting just enough energy to sinter the powder spherules without permitting a melt pool which might flow away from the trace. It’s a precise, carefully controlled process operating in an inert gas environment, but floor-ready machinery has evolved to the point where metal 3D printing can be considered a true manufacturing process…”rapid prototyping” is just one application.
SLS is mature enough that the technology is beginning to see production applications. TRUMPF, for example, has entered a joint venture with Italy’s biggest laser manufacturer SISMA S.p.A., to co-develop production systems for the 3D printing of metal components. TRUMPF originally entered the additive manufacturing sector in the year 2000, however, with companies from several industry sectors now qualifying components and products for additive manufacturing, TRUMPF is working on rapid entry into the market. “Many machines on the market today are aimed more at prototype construction,” explains Dr. Peter Leibinger, head of TRUMPF Laser Technology. “In the future, however, the most important criterion where additive manufacturing lines are concerned will be their suitability for industrial applications.” The target markets of the joint venture are the industrial sector as well as jewellery, fashion and the lucrative dental market.
CAN ADDITIVE PROCESSES REPLACE MACHINING?
That’s the core issue in the debate about the future of additive as a metalworking process. Speed and finish are still areas where subtractive (machining) processes maintain an edge, but the gap is narrowing. One way to bridge the gap is with hybrid technology. DMG MORI has developed a hybrid machine incorporating the firm’s 5-axis milling technology with a generative laser deposition welding head, the LASERTEC 65 Additive Manufacturing. The system deposits material using a powder nozzle and sinters it on the part with a flying laser head, a process which DMG MORI claims can speed the deposition process by 20 times over a powder bed system. In production, the system will machine the major portion of a part and add detail and complex structures with the deposition head. The additively-made portions can then be machined. The ability to machine post-deposition allows the part designer and programmer to specify faster deposition rates and minimize the amount of deposition to reduce cycle times.
Interest in hybrids is growing. Matsuura Machinery Corporation has announced that its LUMEX Avance-25 Metal Laser Sintering Hybrid Milling Machine has entered the North American market (U.S. and Canada) through a distribution agreement with Mitsubishi. The hybrid machine is the result of five years of research and development (R&D). Like other laser sintering machines, the LUMEX Avance-25 binds thin layers of metal powder using a laser, but also mills for higher accuracy as well as complex geometry.
The machine accommodates a maximum workpiece size of 250 x 250 x 180mm. Hybrids are based on current 5-axis machine technology, but could additive manufacturing be retrofit on an existing machine? Hurco has announced that the company recently filed a U.S. patent application for new technology combining 3D printing and CNC machining. “We designed an additive manufacturing adapter that, in combination with proprietary Hurco control software, effectively turns a CNC milling machine into a 3D printer,” said Gregory Volovic, President of Hurco Companies, Inc.
This additive manufacturing technology permits Hurco machine tools to achieve 3D printing directly on the machine tool without the need for a separate 3D printer. Hurco is working on expanding the development to include other additive manufacturing processes.
The company has not announced a production date for the retrofit technology; visitors to IMTS Chicago in September will be looking for more details.
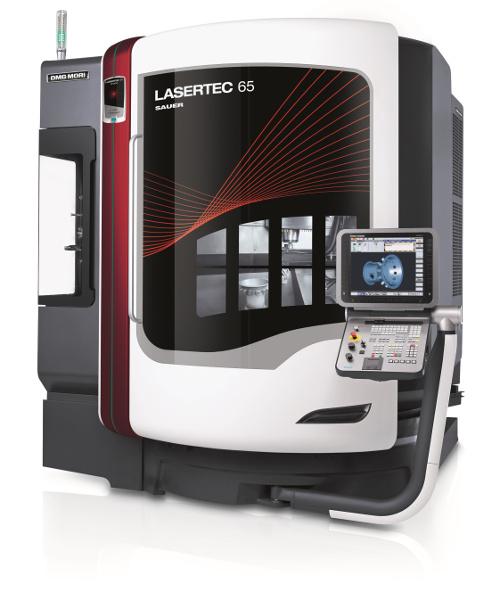
DMG MORI has developed a hybrid additive/ machining centre called the LASERTEC65 AdditiveManufacturing that combines a powder deposition head with a five-axis machining centre. One strength of this process is the option to successively build up layers of different materials. Wall thicknesses of 0.1 mm to 5 mm are possible depending on the laser and the nozzle geo metry. Complex 3D contours can also be generated in layers without supports. The individual layers can then be accurately machined before the areas become inaccessible to a cutter or other tools due to the component geometry. The combination of the two processes is a sensible choice for repair work and the production of moulds as well as parts for the energy and aerospace sectors.
Another emerging technology for large part production is electron beam deposition. Sciaky, Inc., a subsidiary of Phillips Service Industries (PSI) has announced that the firm will become an equipment vendor, offering its electron beam additive manufacturing (EBAM) systems for purchase. Sciaky has predominantly offered its exclusive additive manufacturing process as a service-only option to manufacturers who required assistance to produce large-scale prototypes and production parts, up to 19 feet in length, made of high-value metals like titanium, tantalum, stainless steel, and Inconel. The technology has been a key driver of several high profile R&D projects involving the U.S. Air Force, Lockheed Martin, DARPA and Boeing. The EBAM process, which has been marketed as Direct Manufacturing (DM), combines computer-aided design (CAD), electron beam welding technology and layer-additive processing.
Starting with a 3D model from a CAD program, Sciaky’s fully-articulated, moving electron beam welding gun deposits metal (via wire feedstock), layer by layer, until the part reaches near-net shape. From there, the near-net shape part requires minor post-production machining. Deposition rates of Sciaky’s EBAM process range from 7 to 20 lbs/hr, depending upon part geometry and the material selected. The build envelope can reach up to 19’ x 4’ x 4’ (L x W x H), allowing manufacturers to produce very large parts and structures, with virtually no waste.
ADDITIVE IN PRODUCTION
Mass production of additive metal parts is the holy grail of 3D technology, and General Electric has announced a major step toward that goal. Jet engines have been a natural market for additive parts: light weight, high value and low volume. GE is co-developing (with CFM of France) a complex next generation turbofan project called LEAP, which will enter airline service in 2016, powering the new Airbus A320neo, Boeing 737 MAX and COMAC (China) C919 aircraft. The LEAP engine promises 16 per cent better fuel efficiency than previous generation engines; achieving this efficiency required very advanced gas dynamics and very precise fuel management. In a significant vote of confidence in SLS technology, GE will mass produce a critical component for the engine: fuel nozzles, which will be built at a new facility in Auburn, Alabama. The production volumes will be significant.
CFM to date has logged total orders and commitments for more than 6,000 LEAP engines. There will be almost 20 fuel nozzles in every LEAP engine produced, thus setting the stage for high, long-term production volume at the Auburn plant. Production will ramp up quickly over the next five years, going from 1,000 fuel nozzles manufactured annually to more than 40,000 by 2020. Announced at the 2014 Farnborough Air Show, the new plant will encompass 300,000 square feet and cost USD 50 million to implement.
Equipment installation will begin in late 2014 and production of additive components will begin in 2015. By the end of 2015, the plant could have as many as 10 printing machines with the potential to grow to more than 50 printers and occupy a third of the facility at full capacity. The operation will also continue to manufacture superalloy machined parts for jet engines. GE expects to hire 300 people when the plant is at full ramp-up later this decade. At press time, the supplier of GE’s additive machinery has not been announced. The technology for metal additive manufacturing is evolving quickly.
Next month, Canadian Metalworking will go in depth to discuss the business case and technical details about introducing additive technology to Canadian production and job shops.
About the Author
subscribe now
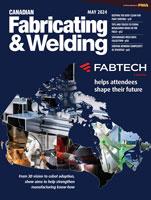
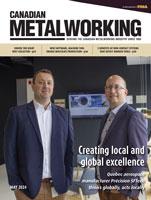
Keep up to date with the latest news, events, and technology for all things metal from our pair of monthly magazines written specifically for Canadian manufacturers!
Start Your Free Subscription- Trending Articles
Sustainability Analyzer Tool helps users measure and reduce carbon footprint
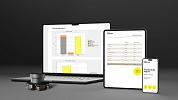
Mitutoyo updates its end-user portal
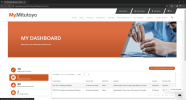
Enhance surface finish with high-speed machining
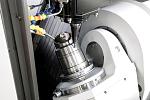
Equispheres secures $20 million investment round
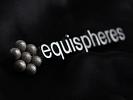
Solid carbide drills produce precision holes in short chipping materials
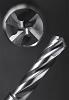
- Industry Events
Automate 2024
- May 6 - 9, 2024
- Chicago, IL
ANCA Open House
- May 7 - 8, 2024
- Wixom, MI
17th annual Joint Open House
- May 8 - 9, 2024
- Oakville and Mississauga, ON Canada
MME Saskatoon
- May 28, 2024
- Saskatoon, SK Canada
CME's Health & Safety Symposium for Manufacturers
- May 29, 2024
- Mississauga, ON Canada